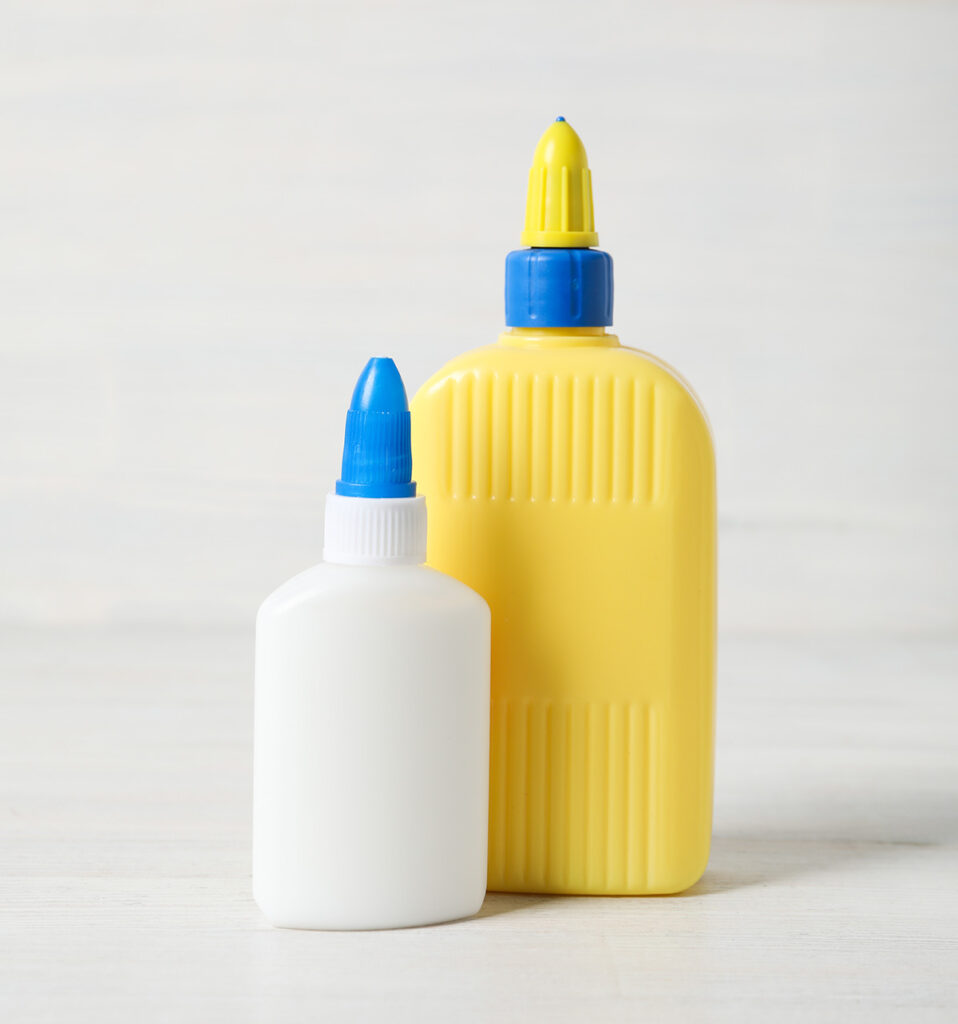
Liquid Ring Pump Applications for the Adhesive Industry
From refinery processes to adhesive application, vacuum equipment plays a pivotal role in various stages of manufacturing. In the initial stages, they are distilled from crude oil. This process yields a higher purity of hydrocarbons like ethane, propane, and octane, which are crucial for producing resins used in adhesive applications.
Vacuum fractional distillation, conducted under subatmospheric pressures before petrochemicals undergo transformation into plastics, rubbers, adhesives, and other chemical compounds, reduces the boiling points of crude oil constituents, enabling efficient separation.
Adhesives undergo a curing process during which they transition from a liquid to a solid state through an irreversible reaction. Especially in the preparation of hot melt adhesives, as well as the water-based adhesives, polyurethanes, polymers, and corrugated adhesives, the resin reaction within a batch reactor only occurs under low pressures. Vacuum application in resin kettle exhausting during curing helps remove excess resin and trapped gasses, ensuring security in structural integrity. Careful control of vacuum strength is crucial to lift bubbles from viscous adhesives without creating voids in the cured resin.
Gas flaring and its associated sulfur dioxide emissions are a significant environmental issue in the petrochemical industry. Flare gas recovery is an alternative waste method that redirects flare gas to a knockout drum. This drum separates gas, water, and oil through gravitational separation and pressure differential. The gas is pulled by vacuum, compressed, and scrubbed, transforming it from flared waste into a valuable resource for distillation or recycling within the plant’s fuel gas system.
Furthermore, vacuum technology is integral to the process of vacuum forming, where heated hydrocarbon polymerized sheets are utilized to create three-dimensional models. In this method, a polymer sheet is heated and positioned over a 3D-printed positive cast. As the sheet is slowly lowered, vacuum suction is applied underneath, evacuating air between the sheet and the cast. This step is crucial to ensure the absence of bubbles for accurately reproduced features from the positive cast onto the finished product. When multiple sheets need to be formed together for thicker walls or higher strength in a vacuum-formed mold or model, adhesive is used and vacuum presses the adhesive tightly between the two sheets for maximum surface contact.
Throughout these diverse applications, the use of adhesives for liquid ring pumps proves to be essential in maintaining optimal performance and efficiency within the vacuum systems involved in each stage of production.